What are regulations on purpose and scope of medical computerized tomography equipment inspection in Vietnam?
What are regulations on purpose and scope of medical computerized tomography equipment inspection in Vietnam? What is content of process of inspecting computerized tomography equipment for medical use in Vietnam?
I have questions about the above issues, hope to be answered according to the provisions of the law.
What are regulations on purpose and scope of medical computerized tomography equipment inspection in Vietnam?
In Section I, Appendix III.9 issued together with Circular 08/2022/TT-BKHCN (effective from July 22, 2022) stipulating the purpose and scope of medical computerized tomography equipment inspection as follows:
1. Purpose
This procedure specifies the verification activity for the validation of medical computed tomography equipment.
2. Scope and subjects of application
This procedure applies to organizations and individuals participating in the inspection of computerized tomography equipment for medical use; State management agencies and other relevant organizations and individuals.
What is content of process of inspecting computerized tomography equipment for medical use in Vietnam?
According to Section I.3, Appendix III.9 issued together with Circular 08/2022/TT-BKHCN (effective from July 22, 2022) inspecting computerized tomography equipment for medical use with contents process as follows:
3.1. diagram
1. Prepare equipment, tools and supplies |
=> |
2.1. Visual inspection |
=> |
3. Inspection result report |
|
|
| |
|
| |
|
|
2.2. Check patient table movement accuracy |
|
4. Inspection certificate |
|
|
| |
|
|
|
|
2.3. Check CT number, uniformity and noise |
|
|
|
|
| |
|
|
|
|
2.4. Check spatial resolution/high contrast |
|
|
|
|
| |
|
|
|
|
2.5. Check spatial resolution/low contrast |
|
|
|
|
| |
|
|
|
|
2.6. Check slice thickness |
|
|
|
|
| |
|
|
|
|
2.7. Check slice center accuracy |
|
|
3.2. Explain
Step 1: Prepare equipment, tools and supplies
Step 2.1: Check the appearance
- Check information about computerized tomography (CT) equipment.
- Check the mode switch and instructions.
- Check the mechanical operation of the systems.
Step 2.2: Check patient table movement accuracy
- Mark the position of an appropriate Fixation Point on the patient table support (fixed part) and the corresponding Point on the patient table (displacement part).
- This test is performed with the patient (weighing approximately 60 kg) lying on a table or using an object of equal weight to the patient fixed to the table in the absence of the patient.
- From the control table of the CT device Control the patient table to move forward the gantry a specified distance. Mark the position after the movement of the patient table and use a protractor to measure the actual displacement of the table, denoted by Lup. Then the control rotates the patient table back to the initial position, marks the position after the displacement and measures the deviation between this position from the initial marker, denoted by Cup.
- Repeat this test procedure with the counter-travel direction of the patient table and take the measurements as above to determine the Backward Movement Distance, denoted Lback, and the return offset . from the original position, denoted by Cback.
Step 2.3: Check CT number, noise and uniformity:
Perform a water phantom scan according to the manufacturer's instructions.
- Place and fix the CT water phantom at the center of the gantry of the device. Mark or record the location of the phantom so that it can be repeated in future tests;
- Scan the phantom through the center area with the shooting parameters according to the manufacturer's instructions. Record these settings in the test report.
- After acquiring the phantom image, select the ROI at the center of the phantom image and 3 ROIs at other locations about 2/3 of the phantom radius towards its edge, at the positions of the 3 clock hands ,6 and 12. ROIs should be circles 20 mm in diameter or squares with sides 20 - 30 mm.
- Determine the average number of CTs, the standard deviation of the number of CTs of each ROI; Record the results in the test report.
Step 2.4: Check spatial resolution/high contrast
Perform a test and evaluation phantom scan according to the manufacturer's instructions:
- Place the test phantom on the patient table and raise the table to align the phantom precisely to the position of the center of rotation and the slice plane; mark or record the location of the phantom so that it can be repeated in future tests; Use a leveling scale to align to ensure that the patient table and gantry do not tilt.
- Scan the phantom in capture mode according to the manufacturer's instructions. Record these settings in the test report.
- Conduct high-contrast/spatial resolution assessment on the basis of phantom images; if a hole phantom is used, determine which row has the smallest hole diameter where all holes can be clearly distinguished from one another and record the hole diameter value; if using a bar phantom, determine which part has the largest number of lines that can still be clearly distinguished between the lines and record the lp/mm value; If using an MTF phantom, determine the MTF cut off value according to the manufacturer's instructions.
Step 2.5: Check low contrast resolution
Perform a test and evaluation phantom scan according to the manufacturer's instructions.
- Place the test phantom on the patient table and align the phantom correctly with the center of rotation and slice plane according to the manufacturer's instructions; Mark or record the location of the phantom so that it can be repeated in future tests.
- Scan the phantom in capture mode according to the manufacturer's instructions; record these set values in the test report.
- Conduct a low-contrast assessment on the basis of the acquired image of the phantom.
Step 2.6: Check the slice thickness
Perform the inspection phantom scan and slice thickness assessment according to the manufacturer's instructions:
- Place the test phantom on the patient's table, use a leveling ruler to check the balance of the phantom and align the phantom correctly with the position of the center of rotation and the slice plane according to the manufacturer's instructions; the angle of inclination of the gantry must be exactly 0°.
- Mark or record the location of the phantom so that it can be repeated in future tests.
- Scan the phantom in capture mode according to the manufacturer's instructions.
Step 2.7: Check slice center accuracy
Perform the inspection phantom scan and slice thickness assessment according to the manufacturer's instructions:
- Place the test phantom on the patient's table, use a leveling ruler to check the balance of the phantom and align the phantom correctly with the position of the center of rotation and the slice plane according to the manufacturer's instructions; the angle of inclination of the gantry must be exactly 0°.
- Mark or record the location of the phantom so that it can be repeated in future tests.
- Scan the phantom in capture mode according to the manufacturer's instructions.
Step 3: Report the inspection results
- The inspection results must be recorded in an inspection record with all contents according to Form 1. The inspection record is issued together with QCVN 12:2016/BKHCN.
- The inspection record must be approved and signed and stamped (if any) by the following members:
+ The representative of the facility using the CT equipment or the person authorized by the establishment.
+ The person assigned by the establishment using the CT equipment to participate and witness the inspection.
+ The person performing the test.
- Based on the data of the test results in the inspection report, the person performing the inspection must calculate and evaluate the working characteristics of the X-ray equipment according to the instructions and make a report. inspection assessment according to Form 2. Report on inspection results issued together with QCVN 12:2016/BKHCN.
Step 4: Certificate of inspection
- The certificate of inspection is only issued to the X-ray equipment after it has been tested and concluded to meet the acceptance requirements.
When the inspected X-ray equipment meets the acceptance requirements, the inspection organization must issue an inspection certificate within 15 working days from the date of approval of the inspection report at the establishment according to Form 3. Certificate of inspection issued together with QCVN 12:2016/BKHCN.
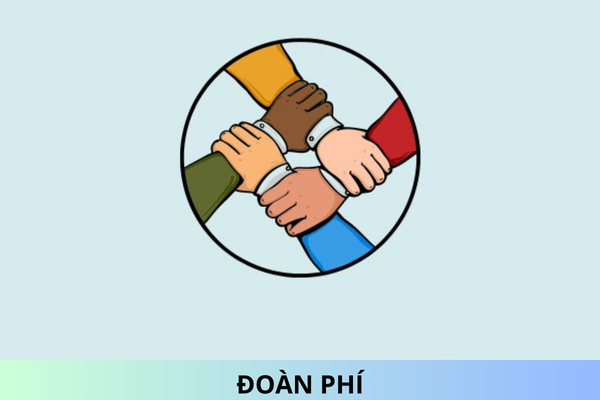
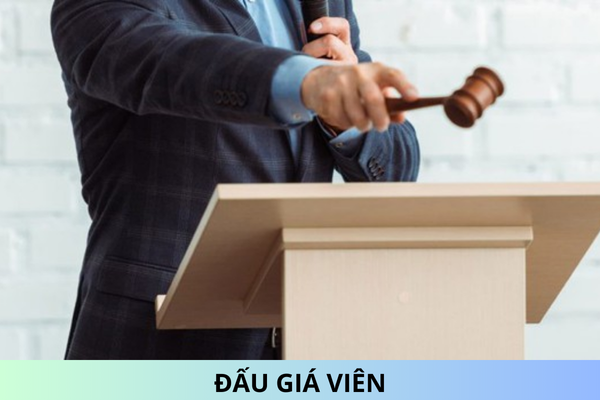
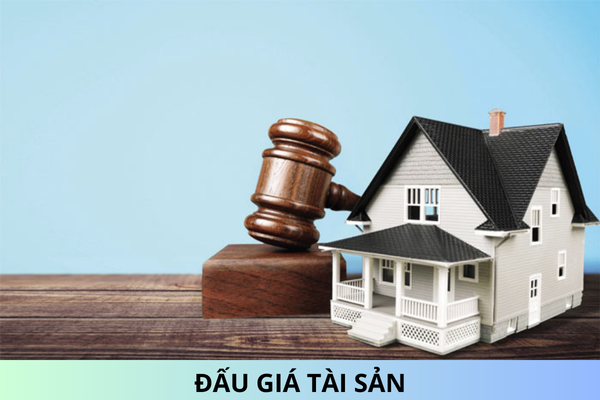
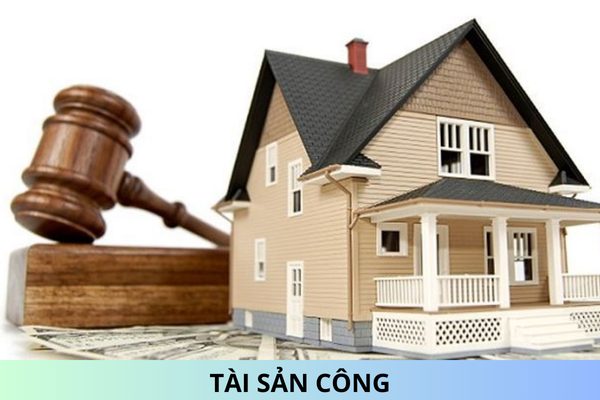
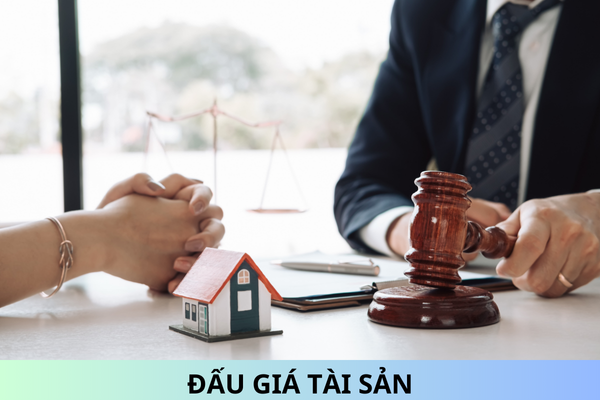
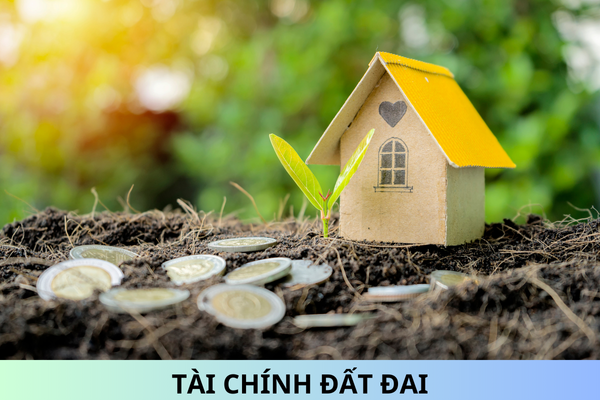
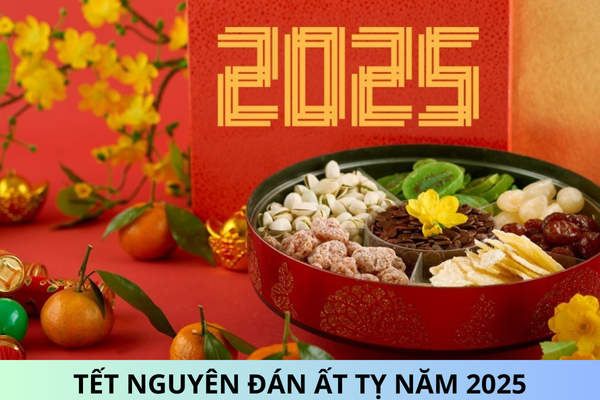
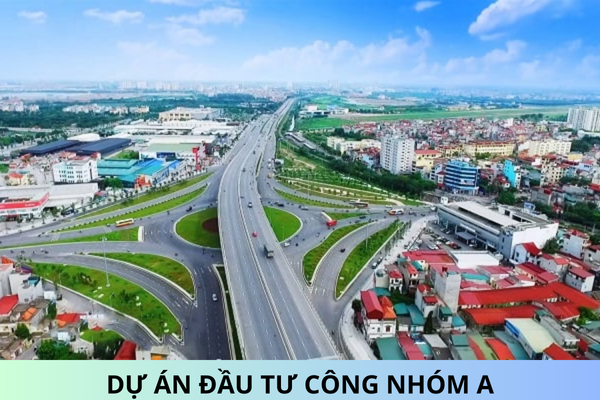
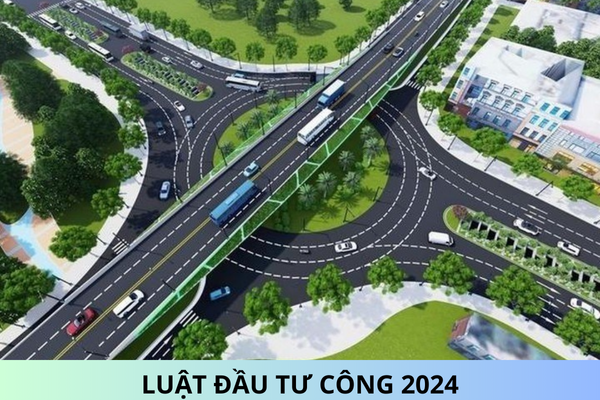
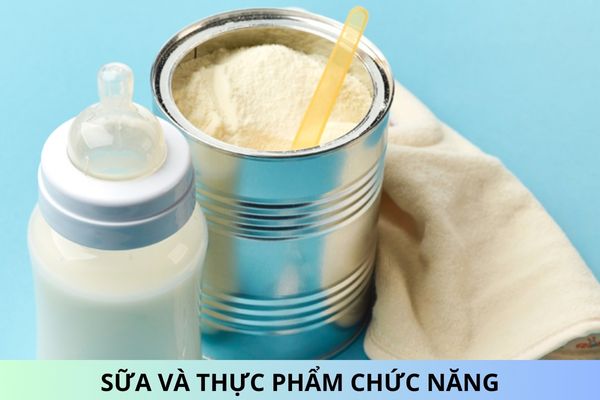