What are regulations on quality testing during drug mixing process in Vietnam?
What are regulations on quality testing during drug mixing process in Vietnam? Thank you!
What are regulations on quality testing during drug mixing process in Vietnam?
Pursuant to Article 9 of the Circular 30/2021/TT-BYT (takes effect from 01/03/2022) stipulating quality testing during drug mixing process in Vietnam as follows:
- If drugs mixed in accordance with Clause 2 Article 2 hereof are mixed in batches, test 100% of the batches based on quality standards approved by heads of medical establishments.
- Medical establishments shall test or send samples to facilities capable of testing drugs as per the law.
What are regulations on quality control during drug mixing process in Vietnam?
Pursuant to Article 8 of the Circular 30/2021/TT-BYT (takes effect from 01/03/2022) stipulating quality control during drug mixing process in Vietnam as follows:
1. For drugs mixed in accordance with Clause 2 Article 2 hereof, quality control shall be carried out as follows:
a) Initial ingredients for mixing drugs must be up to standards (not expired, attached by certificate of analysis, invoice, certificate of origin);
b) Packing materials and printed packages must be kept in separate areas and distributed depending on mixing demands;
c) Semi-finished products (if any) awaiting packaging shall be labeled and preserved as per the law before being subject to quality control and subsequent stages;
d) Control mixing process
- Control at weighing station for medicinal ingredients: before weighing and distributing ingredients, inspect sanitation, temperature, humidity, ensure clean weighing and distribution areas and accurate results. Sterile ingredients must be weighed and distributed in sterile areas;
- Control mixing process: have sufficient number of persons mixing drugs and have appropriate solutions for monitoring all actions during mixing process. All employees must wear proper PPE before mixing drugs; mixing environment and conditions must meet regulations. All mixing equipment must be inspected for sanitation conditions before use and during mixing process. All ingredients, packaging of semi-finished products, precision machinery, packing rooms and assembly lines in use must bear labels containing name of the drugs being mixed and batch number. Inspect, control, and record all inspection results during mixing process and environmental control as per mixing process.
dd) Control labeling and packaging activities: control primary packaging materials and pre-printed packaging before mixing, labeling and packaging activities must be physically separated to prevent any confusion, separate and safe preservation areas must be prepared for finished products awaiting distribution.
2. For drugs mixed in accordance with Clause 3 Article 2 hereof, quality control shall be carried out as follows:
a) All finished products before being mixed must be inspected visually and unexpired;
b) Control mixing, packaging, labeling process by assigning one control person for every person mixing drugs.
Best regards!
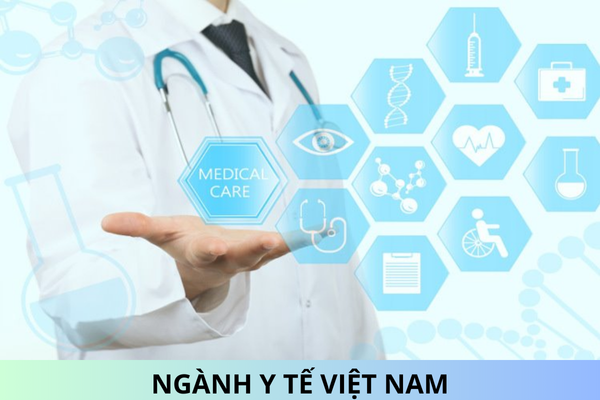
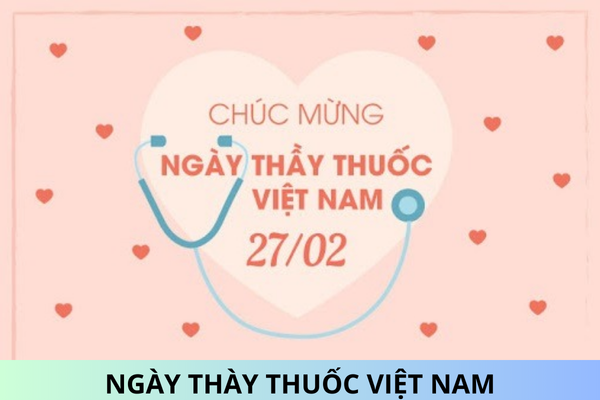
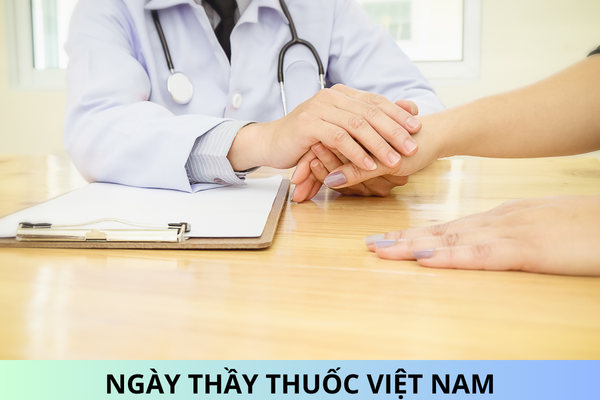
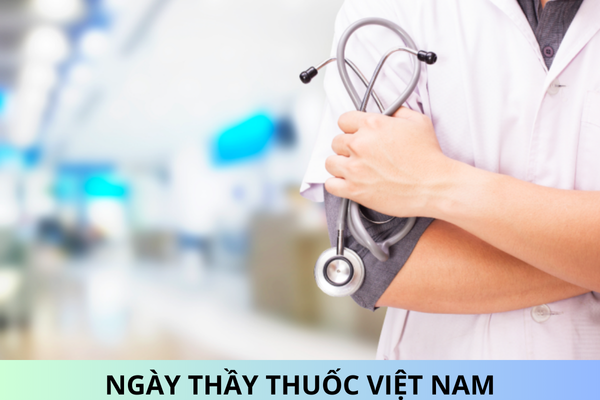
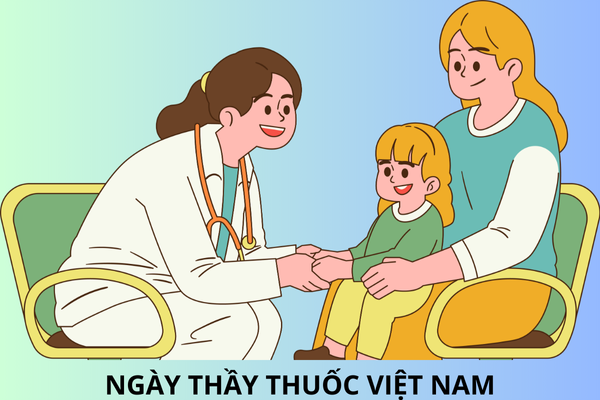
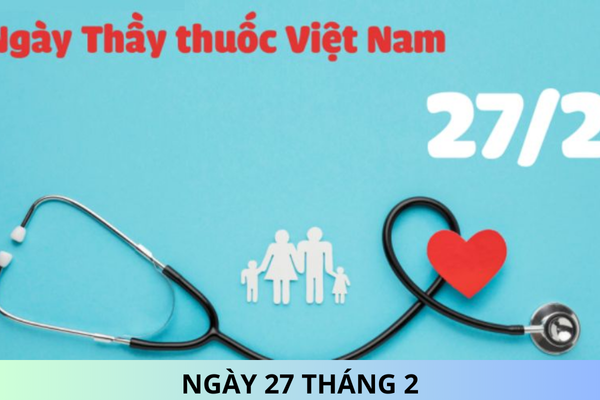
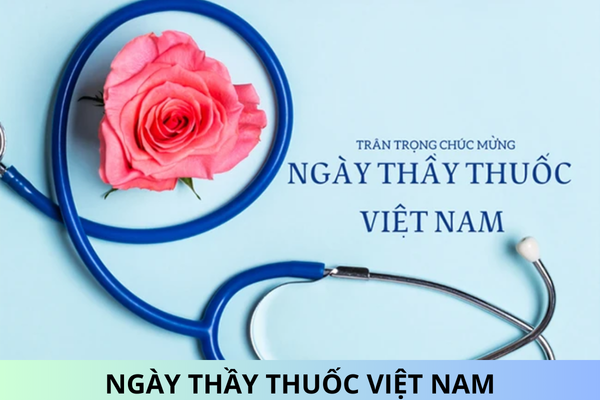
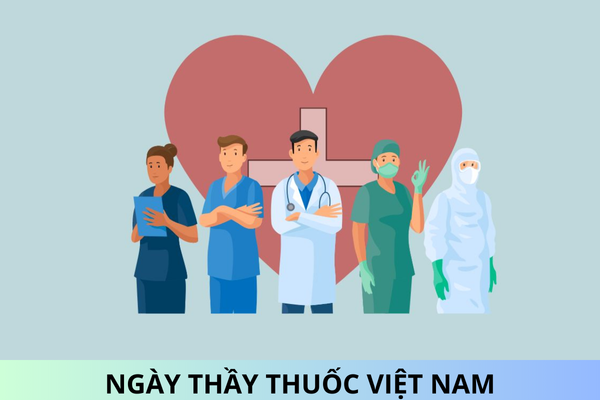

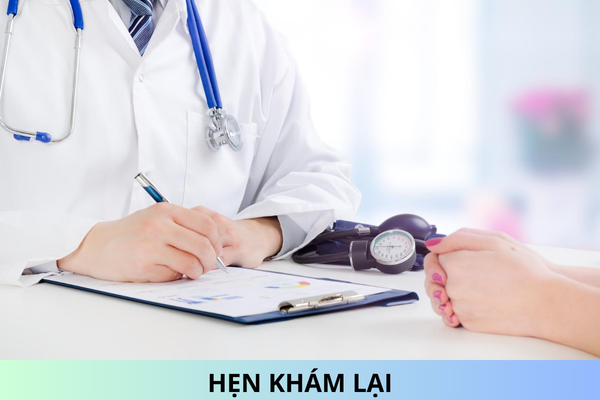